Introduction
Nature is a vital ingredient in ensuring healthy people, healthy business and a healthy planet.
Yet it faces challenges such as mass extinction rates and pressure on land, water, oceans, climate and biodiversity to feed and house 9 billion people by 2050. Our Nature Action work moves the focus to the global commons and the biosphere, ensuring efforts to drive action across government, business, and civil society, including the development of science-based targets, guidance for consistent and credible business actions to nature positive such as high integrity nature-based solutions. We support members and engage and act directly on the fast-moving nature agenda.
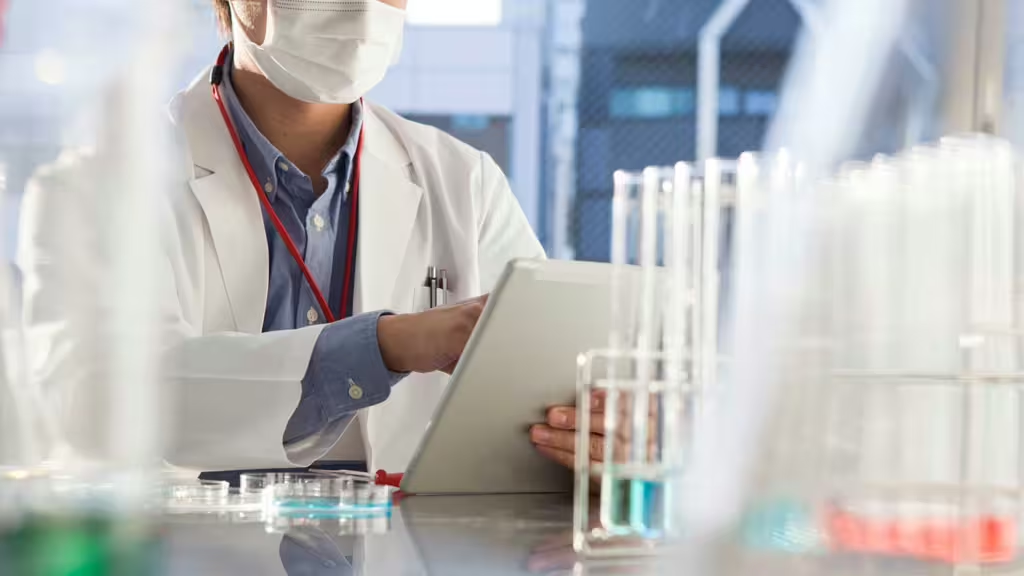
Pharma companies mark a key milestone on their journey to nature positive
24 October, 2024
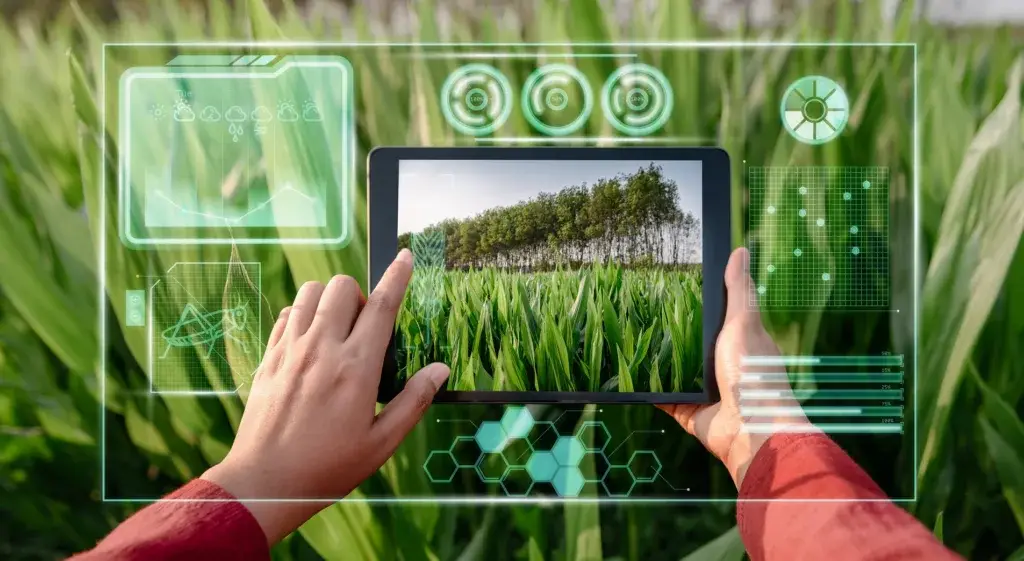
Harmonizing nature-related metrics for business
23 October, 2024
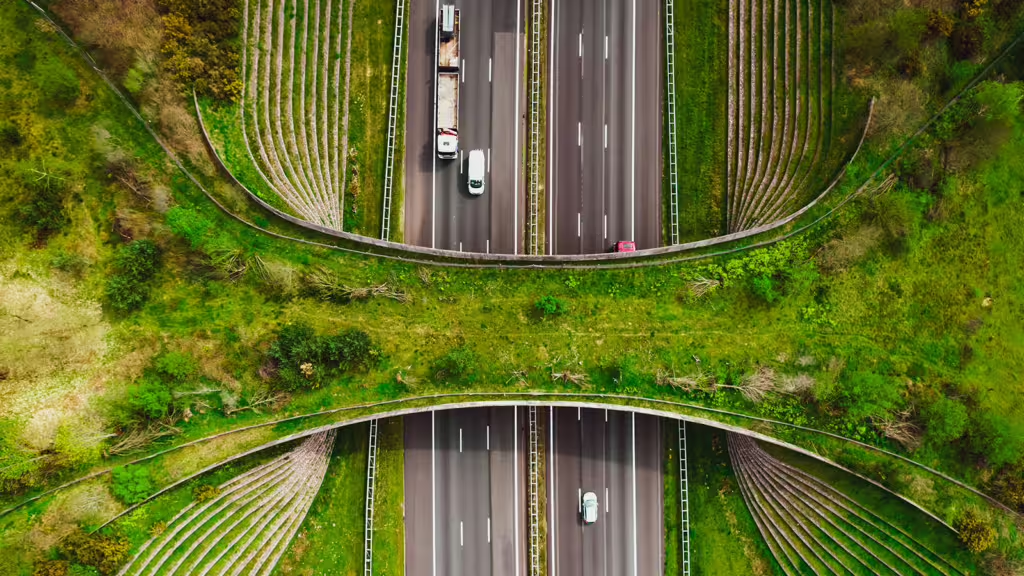
Unleashing corporate target-setting for nature at scale
20 September, 2024
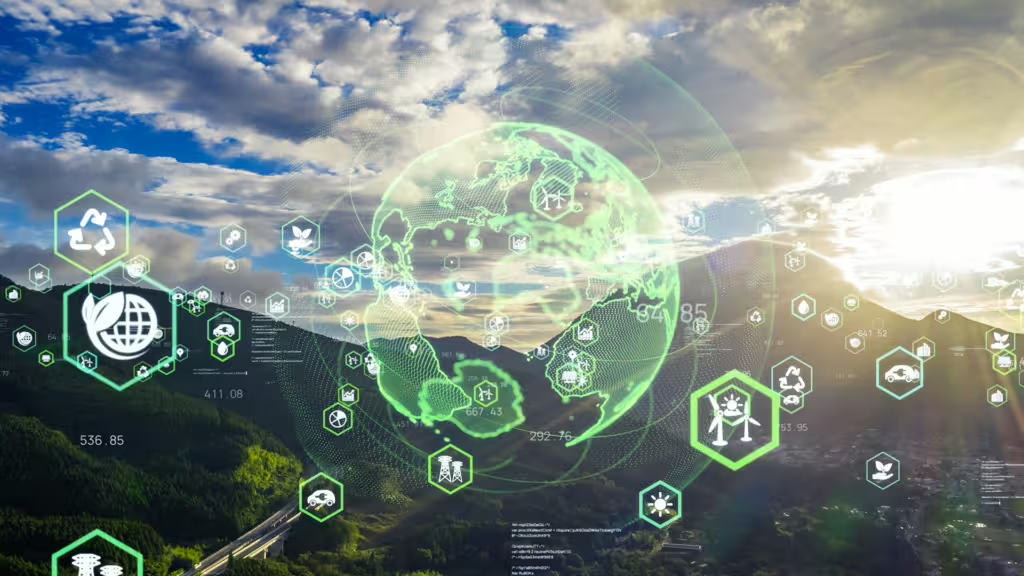
Harmonizing the use of nature-related metrics by corporations
23 October, 2024
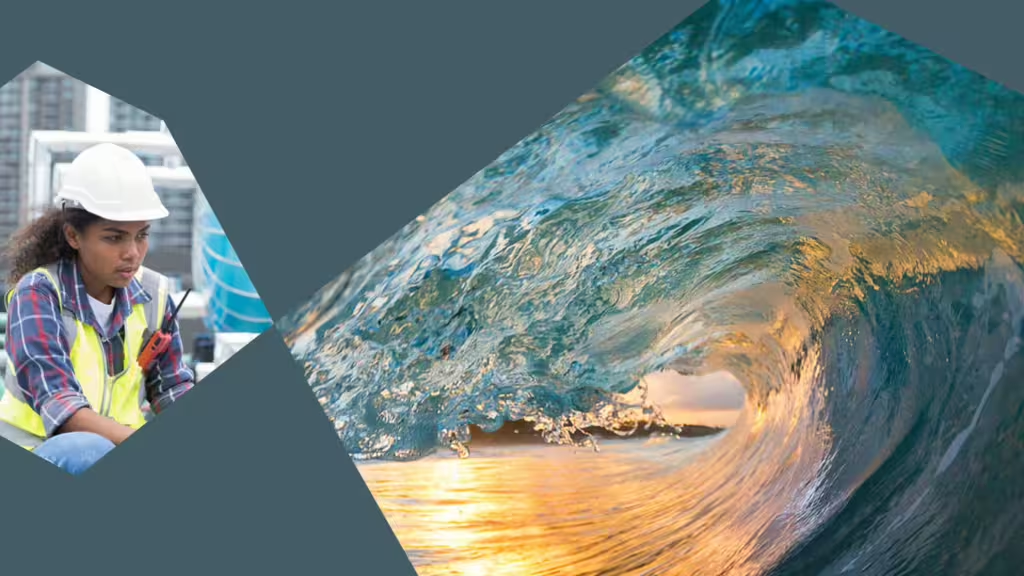
Towards Planet Positive Chemicals: A Chemical Transformation Roadmap
1 October, 2024
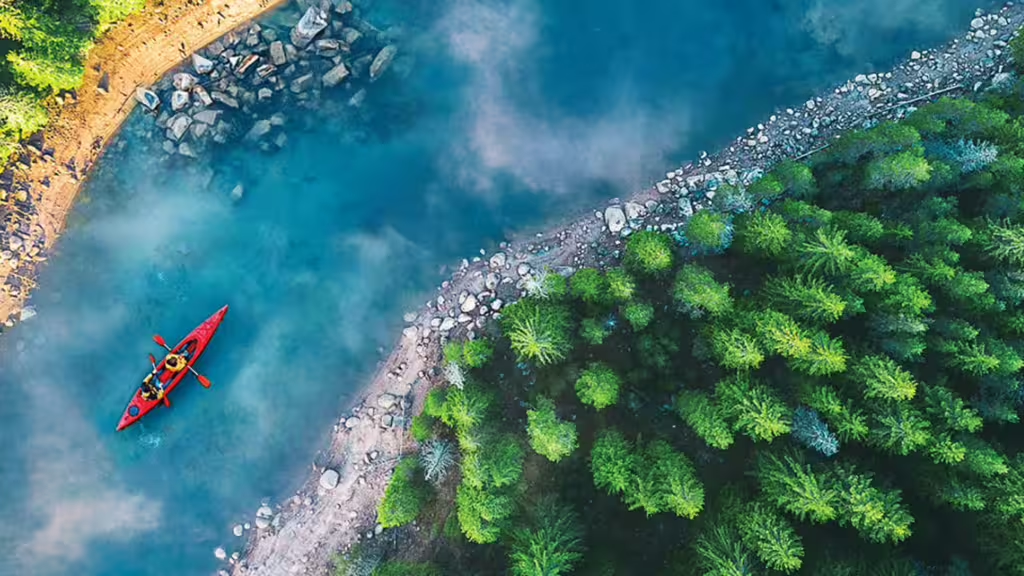
Roadmap to Nature Positive: Examples from the built environment industry
24 September, 2024